Totul despre foraj orizontal
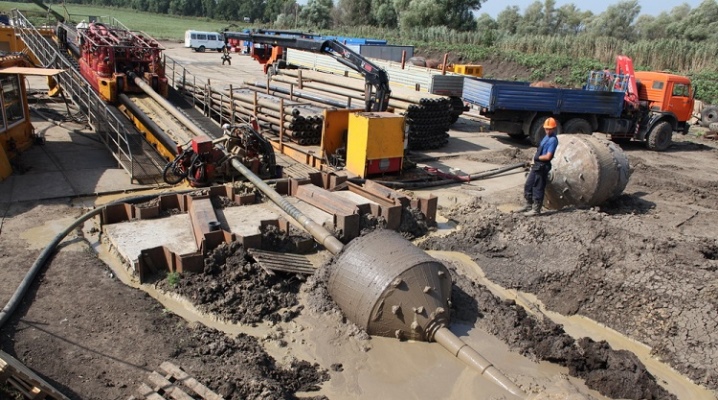
Forajul orizontal este unul dintre tipurile de sonde. Tehnologia a devenit larg răspândită în industria construcțiilor, industria petrolului și gazelor, precum și atunci când se lucrează în condiții urbane aglomerate. Să luăm în considerare mai detaliat care este esența metodei și care sunt etapele principale pentru acest tip de foraj.
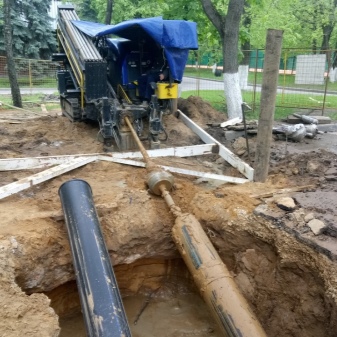
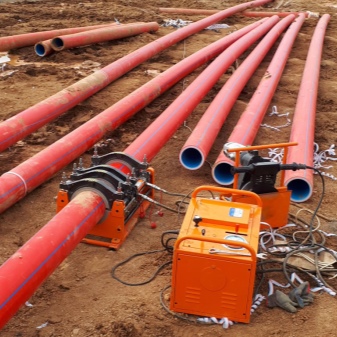
Ce este?
Forarea direcțională orizontală (HDD) este un tip de foraj fără șanț care ajută la conservarea suprafeței peisajului (de exemplu, patul drumului, elementele de amenajare a teritoriului etc.). Această tehnică a apărut în anii 60 ai secolului trecut și este populară astăzi. Tehnica face posibilă reducerea costurilor de foraj sau, mai degrabă, restaurarea peisajului după acest proces.
În medie, costul muncii este redus de 2-4 ori.
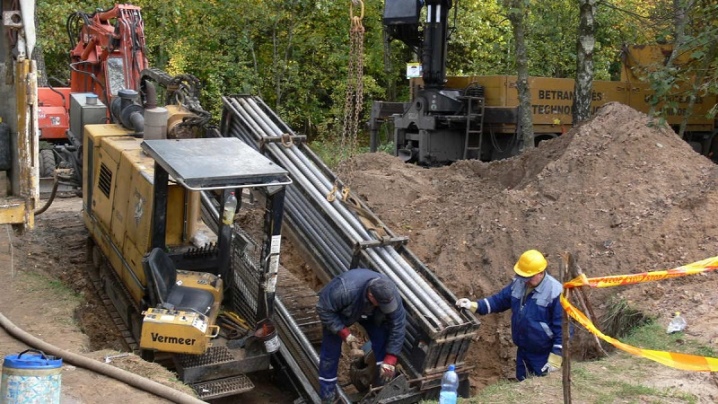
Caracteristicile tehnologiei
În cuvinte simple, atunci principiul metodei se reduce la crearea a 2 perforații în pământ (gropi) și a unui „pasaj” subteran între ele folosind o așezare a țevii înclinată orizontal. Această tehnologie este utilizată și în cazurile în care este imposibil să săpați un șanț (de exemplu, pe obiecte valoroase din punct de vedere istoric). Tehnica presupune realizarea unor lucrări pregătitoare (analiza solului, pregătirea a 2 locuri - la punctele de intrare și ieșire din șanț), formarea unui puț pilot și extinderea ulterioară a acestuia în funcție de diametrul conductei. În etapa finală a lucrării, țevile și/sau firele sunt trase în șanțurile rezultate.
Cu HDD, atât țevile din plastic, cât și cele din oțel pot fi așezate în șanț. Primul poate fi fixat într-un unghi, în timp ce cel din urmă poate fi fixat doar pe o cale dreaptă. Acest lucru permite utilizarea țevilor din polipropilenă în șanțuri sub corpurile de apă.
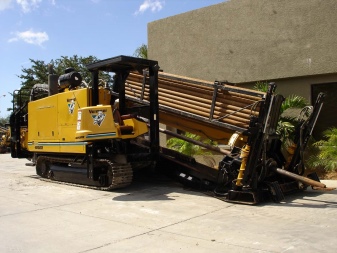
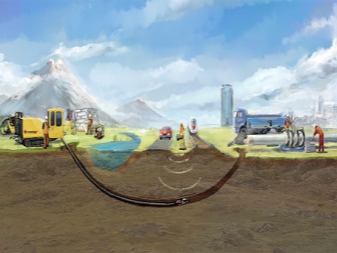
Găurirea orizontală este eficientă în rezolvarea următoarelor sarcini:
- Pozarea cablurilor electrice, gazelor și conductelor la obiecte;
- obtinerea de sonde pentru productia de petrol si extragerea altor minerale;
- renovarea comunicațiilor care au suferit uzură;
- formarea autostrăzilor subterane.
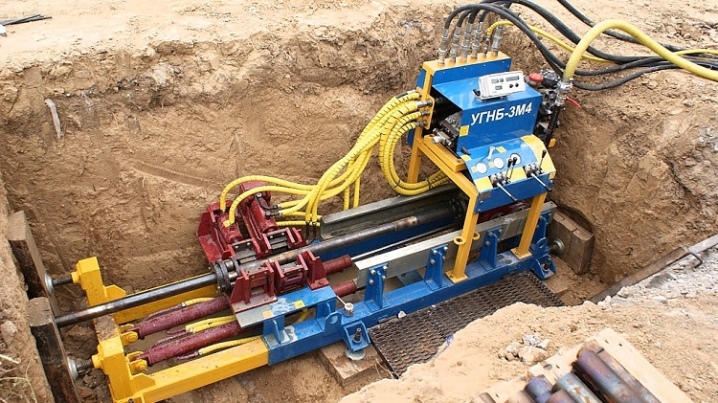
Pe lângă aceste economii, această tehnică de foraj are și alte avantaje:
- distrugerea minimă a suprafeței pământului (se fac doar 2 perforații);
- reducerea timpului de lucru cu 30%;
- reducerea numărului de muncitori din brigadă (sunt necesare 3-5 persoane);
- mobilitatea echipamentelor, este ușor de instalat și transportat;
- capacitatea de a efectua lucrări în orice teritoriu (centre istorice, pe teritoriul trecerii liniilor de înaltă tensiune) și sol;
- capacitatea de a conserva solul fără a-i deteriora straturile fertile;
- punerea în aplicare a muncii nu necesită o schimbare a ritmului obișnuit: mișcare suprapusă etc.;
- nici un rău pentru mediu.
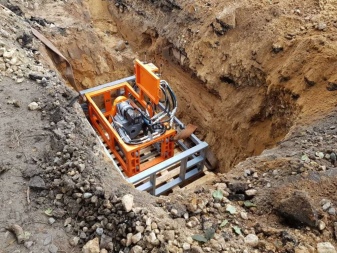
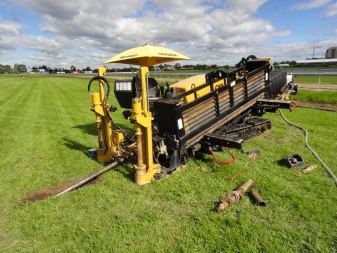
Beneficiile descrise contribuie la popularitatea și adoptarea pe scară largă a metodei HDD. Cu toate acestea, are și dezavantaje.
- Cu ajutorul instalațiilor standard pentru foraj adânc, este posibilă așezarea țevilor cu o lungime de cel mult 350-400 de metri. Dacă trebuie să așezați o conductă mai lungă, trebuie să faceți îmbinări.
- Dacă este necesar să instalați țevi mai lungi în subteran sau să le treceți la adâncimi mari, metoda fără șanț va fi prea costisitoare.
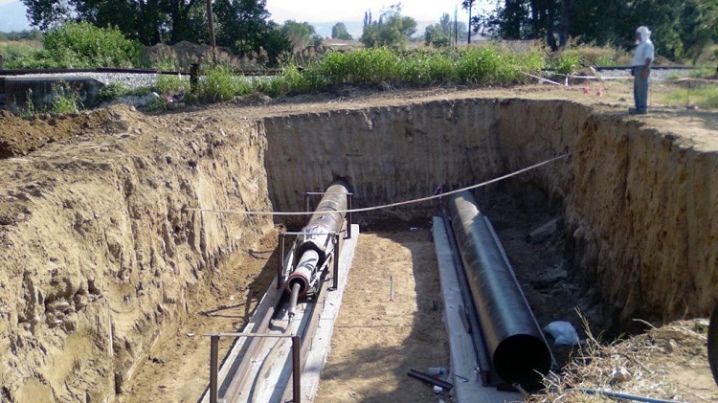
Echipamente
Pentru a realiza HDD, se folosesc mașini și unelte care pot străpunge straturile superioare ale solului și pot merge mai adânc.Pe baza volumului de lucru și a tipului de sol, acestea pot fi burghie speciale pentru rocă, burghie cu motor sau mașini de găurit. Primele 2 variante sunt de obicei folosite pentru uz personal, in timp ce masinile de gaurit sunt folosite pe obiecte mari, soluri solide si dure.
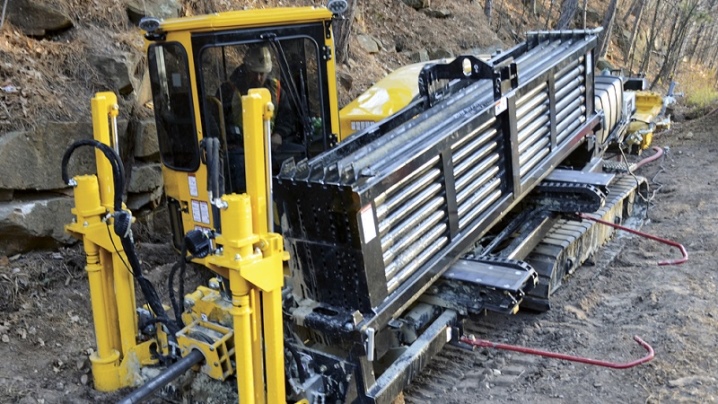
Mașini
O mașină de forat sau instalație HDD este un tip de echipament industrial care funcționează pe un motor diesel. Principalele elemente funcționale ale mașinii sunt o stație hidraulică, un cărucior, un panou de control. Acesta din urmă permite operatorului să controleze funcționarea și mișcarea mașinii și arată ca un panou de control special. Crearea unui șanț în sine este posibilă datorită unui burghiu. În timpul rotației, burghiul se încălzește, ceea ce este plin de defecțiunea sa rapidă. Acest lucru poate fi evitat prin răcirea regulată a piesei metalice cu apă. Pentru aceasta, se folosește un furtun de alimentare cu apă - un alt element al mașinii de găurit.
Echipamentul de foraj este clasificat în funcție de limita forței de tragere (măsurată în tone), lungimea maximă a forajului și diametrul găurii de foraj. Pe baza acestor parametri, se calculează puterea burghiului. Un analog mai compact al unei instalații de foraj este un foraj cu motor. Scopul său principal este de a efectua mici lucrări de pământ. Cu toate acestea, partea de perforare a procesului de găurire, în unele cazuri, se realizează destul de ușor și rapid cu un burghiu cu motor. Deoarece găuritul cu motor funcționează ca echipament cu melc, este adesea numit o mașină cu melc presat. Această platformă include un burghiu, tijă și motor.
Găurirea cu un motor de găurit este posibilă chiar și de către o singură persoană, dispozitivele diferă în funcție de tipul de putere și sunt împărțite în profesional și pentru uz privat.
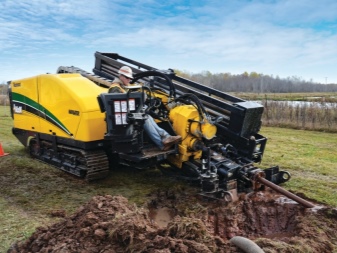
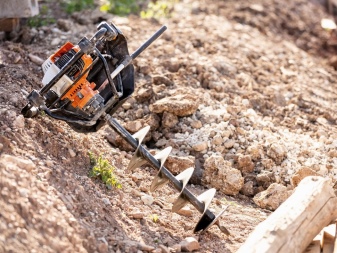
Sisteme de localizare
Un astfel de sistem este necesar pentru a controla cu precizie traiectoria capului de foraj și ieșirea acestuia la locul celei de-a doua puncție. Este o sondă atașată la capul de foraj. Locația sondei este monitorizată de lucrători care folosesc localizatoare.
Utilizarea unui sistem de localizare previne ciocnirea capului de foraj cu obstacole naturale, de exemplu, depozite de soluri dense, ape subterane, pietre.
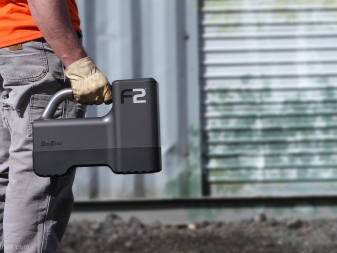
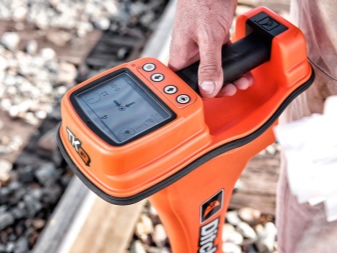
Instrumente de sprijin
Acest tip de instrumente devine necesar în etapa de perforare a solului. Tije uzate, scule cu șurub filetat, expansoare, pompe. Alegerea unui instrument specific este determinată de tipul de sol și de etapele de lucru. Uneltele auxiliare includ, de asemenea, cleme și adaptoare, a căror sarcină principală este de a ajuta la obținerea unei conducte de lungimea necesară. Expansoarele sunt folosite pentru a obține un canal cu diametrul necesar. Apa este furnizată instalației cu ajutorul unui sistem de pompă. Generatoarele asigură funcționarea neîntreruptă a echipamentului, iar sistemul de iluminat permite forarea chiar și pe întuneric.
Uneltele sau consumabilele auxiliare includ vaselina cupru-grafit. Este folosit pentru lubrifierea articulațiilor tijelor de foraj. Forarea orizontală implică în mod necesar utilizarea bentonitei, a cărei calitate afectează în mare măsură viteza de lucru, fiabilitatea șanțului și siguranța mediului. Bentonita este o compoziție multicomponentă pe bază de aluminosilicat, caracterizată prin dispersie crescută și proprietăți hidrofile. Restul ingredientelor soluției și concentrația lor sunt selectate pe baza analizei solului. Scopul folosirii bentonitei este de a întări pereții șanțului, pentru a evita vărsarea solului.
De asemenea, soluția previne aderența solului la echipament și răcește elementele rotative.
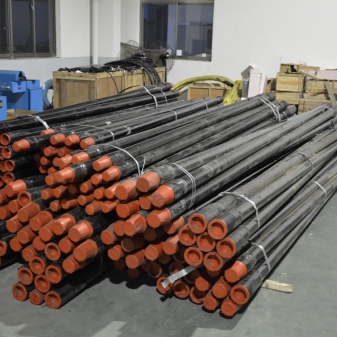
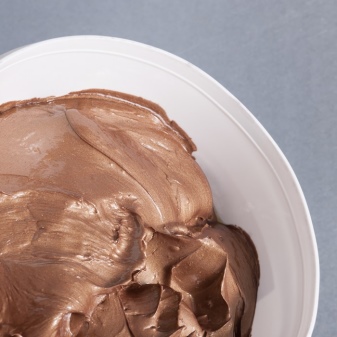
Descrierea pas cu pas a procesului
HDD-ul se desfășoară în mai multe etape, iar schema generală de lucru arată astfel:
- intocmirea documentelor de proiect, care reflecta toate calculele necesare;
- coordonarea proiectului cu proprietarul șantierului (dacă este un teritoriu privat) și autorități (dacă este vorba de realizarea lucrărilor la dotări municipale);
- gropi de săpat: una la începutul lucrărilor, a doua la punctul de ieșire a conductei;
- așezarea echipamentelor necesare cu ajutorul instalațiilor de foraj;
- finalizarea lucrărilor: rambleul gropilor, dacă este necesar - refacerea peisajului la locul gropilor.
Înainte de a face o gaură în pământ, trebuie avut grijă să pregătiți peisajul. Pentru a instala echipamente universale de foraj, veți avea nevoie de o suprafață plană de 10x15 metri, aceasta este situată direct deasupra locului perforației de admisie. O poți face singur sau folosind un echipament special. Asigurați-vă că există ocoluri către acest site. După aceea, are loc livrarea și instalarea echipamentelor de foraj.
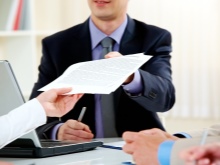
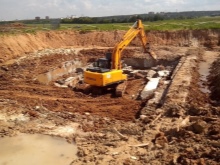
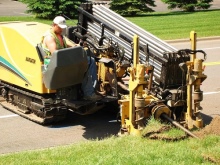
Pe lângă mașina HDD, vor fi necesare echipamente pentru prepararea nămolului de bentonită. Este folosit pentru a întări pereții șanțului și pentru a îndepărta pământul din canal. Instalația pentru nămol de bentonită este plasată la o distanță de 10 metri de mașina de găurit. În apropierea punctelor de perforare prevăzute se creează mici adâncituri în cazul excesului de mortar.
Etapa de pregătire presupune şi instalarea şi verificarea comunicaţiilor radio între muncitorii brigăzii, analize de sol. Pe baza acestei analize, se selectează una sau alta rută de foraj. Zona de foraj trebuie protejată cu bandă galbenă de avertizare. Apoi se instalează echipamentul de foraj și tija pilot. Este fixat în punctul în care capul de foraj pătrunde în pământ.
Un pas important este asigurarea sculelor cu ancore pentru a evita deplasarea în timpul HDD-ului.
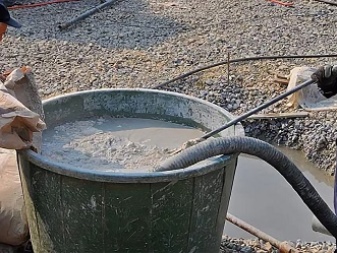
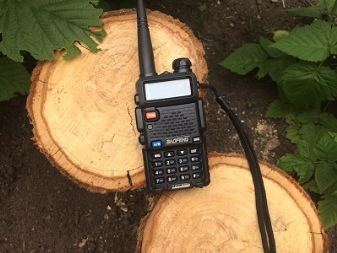
După finalizarea etapei pregătitoare, puteți trece direct la forare. Mai întâi, se formează un puț pilot cu o secțiune transversală de 10 cm, apoi echipamentul este re-depanat și se ajustează înclinarea capului de foraj - ar trebui să aibă un unghi de înclinare de 10-20 de grade față de linia orizontului. Un puț pilot este o perforație de antrenament, fără a cărei formare forarea fără șanț este inacceptabilă. În acest moment, se verifică funcționarea și funcționalitatea sistemelor și se evaluează caracteristicile mișcării forajului.
În stadiul formării unei găuri pilot, este necesar să reglați instrumentul pentru unghiul de înclinare al solului și, de asemenea, să verificați poziția capului de foraj în raport cu linia peisajului. Pentru orice eventualitate, în gropi se formează coturi. Ele vor fi utile dacă ape subterane sau lichide bentonite se găsesc în volume mari. Acesta din urmă va preveni prăbușirea șanțului și frânarea burghiului din cauza aderenței solului la acesta, supraîncălzirea echipamentului.
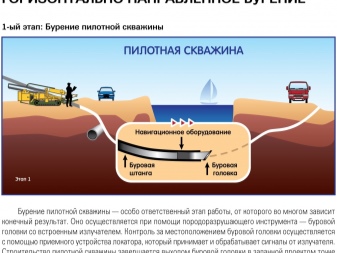
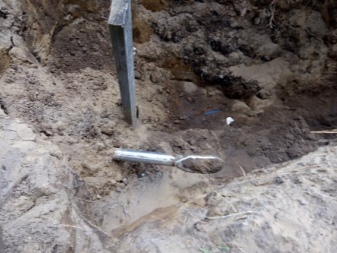
Când pregătiți, este important să faceți calcule precise pentru a nu deteriora conductele de conducte așezate anterior. Distanța minimă de la conducte trebuie să fie de 10 metri. Apoi începe procesul de burghiu care trece printr-o anumită traiectorie și la fiecare 3 metri este necesar să se controleze și să corecteze direcția instrumentului. Când burghiul atinge adâncimea necesară, începe să se miște orizontal sau cu o pantă ușoară - așa este așezat un șanț de lungimea necesară. După ce burghiul a depășit lungimea necesară, acesta este îndreptat în sus spre ieșire. Desigur, punctul celei de-a doua gropi este calculat în avans, iar în acest moment site-ul este pregătit preliminar.
Pasul final este să scoateți unealta originală de pe sol și să extindeți gaura cu un alez sau un rimmer. Este instalat în locul burghiului și vă permite să măriți diametrul canalului pilot. În timpul deplasării expandorului, se asigură controlul și, dacă este necesar, corectarea traiectoriei mișcării sculei la fiecare 3 metri.
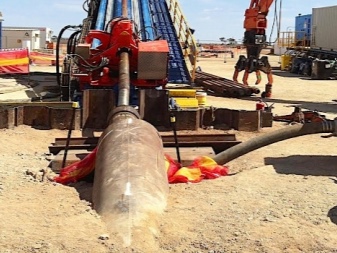
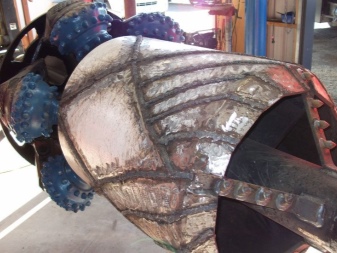
Rimmer se deplasează pe o traiectorie opusă direcției burghiului, adică de la a doua puncție la prima. În funcție de diametrul necesar al șanțului, alezul poate trece prin acesta de mai multe ori. Diametrul canalului depinde de diametrul țevilor - în medie, ar trebui să fie cu 25% mai lat decât diametrul țevilor care sunt așezate. Dacă vorbim de țevi termoizolante, atunci lățimea diametrului canalului ar trebui să fie cu 50% mai mare decât diametrul țevilor.
Dacă se obține o presiune mare a solului în canal și există o probabilitate crescută de prăbușire, atunci se produce o distribuție uniformă a bentonitei. După ce se întărește, nu este exclus doar riscul de prăbușire, ci și tasarea solului. Pentru intrarea și trecerea mai ușoară a sculei prin sol, se folosește un fluid de foraj special de înmuiere. Cu metoda HDD, se acordă o mare atenție riscului de vărsare a solului. În acest sens, rezistența conexiunii conductelor este monitorizată suplimentar, astfel încât acestea să nu se rupă sub greutatea solului care se prăbușește.
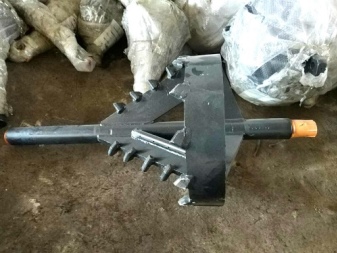
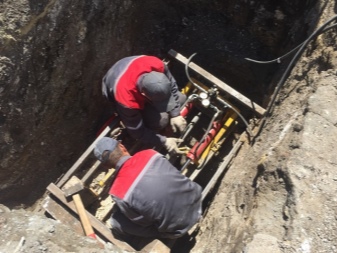
După ce șanțul orizontal este gata, încep să instaleze țevi în el. Pentru a face acest lucru, îi sunt atașate console și pivotări, cu ajutorul cărora va fi posibilă strângerea conductei în canal. La începutul țevii este atașat un cap, pentru care pivotul va fi deja fixat. Conductele sunt, de asemenea, îmbinate prin pivot, în timp ce echipamentul de foraj în sine este oprit. Pentru îmbinare, ei recurg la utilizarea adaptoarelor speciale.
Pentru puțuri de dimensiuni mici și tragerea de țevi de plastic cu diametru mic, se folosește forța mașinii de găurit. După așezarea țevii într-un șanț orizontal, procesul HDD este considerat finalizat.
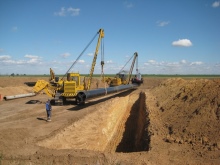
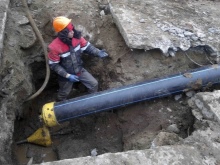
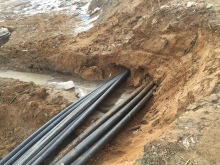
Scopul aplicatiei
HDN este potrivit pentru așezarea conductelor de protecție în interiorul cărora trec cabluri telefonice, de fibră optică și de alimentare; pentru instalarea unei conducte în interiorul căreia se deplasează apa pluvială și de canalizare, precum și apa potabilă. În cele din urmă, conductele de apă și conductele de petrol și gaze pot fi, de asemenea, așezate folosind metoda HDN.
Tehnica este folosită și în acele cazuri când este necesară reducerea bugetului pentru reparații sau reducerea numărului de muncitori. Scăderea costurilor financiare se datorează absenței necesității refacerii peisajului după forare, precum și automatizării maxime a procesului. Optimizarea dimensiunii echipei de lucru devine posibilă datorită faptului că lucrătorii sunt de fapt necesari doar pentru a opera mașina.
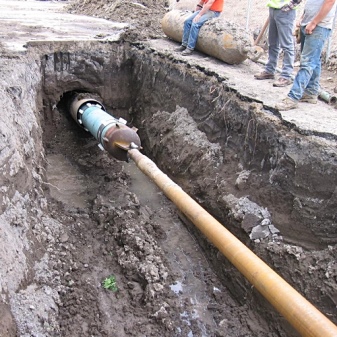
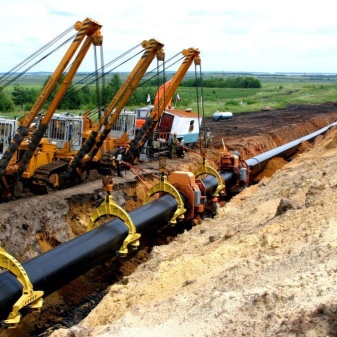
Tehnica este eficientă atunci când se instalează conducte în soluri nisipoase, lutoase și argiloase. Utilizarea tehnologiei descrise este justificată dacă șanțul trece pe sub autostrăzi, în zone valoroase din punct de vedere istoric sau sub apă. În acest din urmă caz, puncția de intrare se face prin gura râului.
Forarea fără șanțuri este eficientă nu numai în zonele urbane dense și centrele istorice, ci și într-o casă privată, deoarece vă permite să păstrați plantațiile și clădirile. De regulă, sistemele de alimentare cu apă și de canalizare sunt amplasate pe proprietatea privată în acest fel.
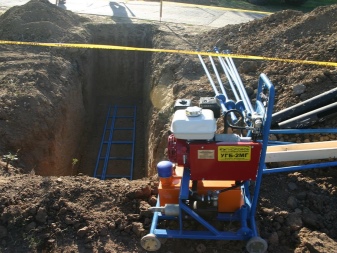
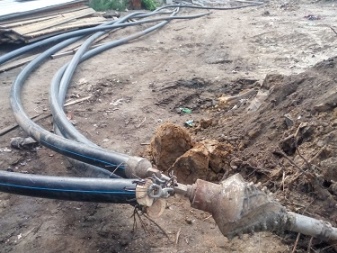
Vedeți următorul videoclip pentru a afla cum funcționează găurirea direcțională orizontală.
Comentariul a fost trimis cu succes.